The Challenge – Machine Design
Client: Automation machine manufacturer
Objective: Scale up production
A client needed to quickly automate a process to scale up the production of a consumable component used in COVID-19 Point of Care Diagnostic Units. As a result, a machine was designed that automatically singulated parts, filled them with saline, verified that the proper amount was dispensed using a vision inspection system, sealed the component, and verified the seal via another vision inspection system.
- Due to the immediate need for a fully automated system to fill and seal the test kits, the project design timeline was highly aggressive. Nevertheless, Sterling Engineering was able to mobilize and assign design engineers to this project within 24 hours.
- The design and detailing were accomplished by utilizing two shifts in less than three (3) weeks, working over 1,000 hours.
- Daily design reviews with all project leads were implemented, resulting in a synchronized, seamless workflow process.
- Through collaboration, our client could respond quickly to meet deadlines in an accelerated timeframe.
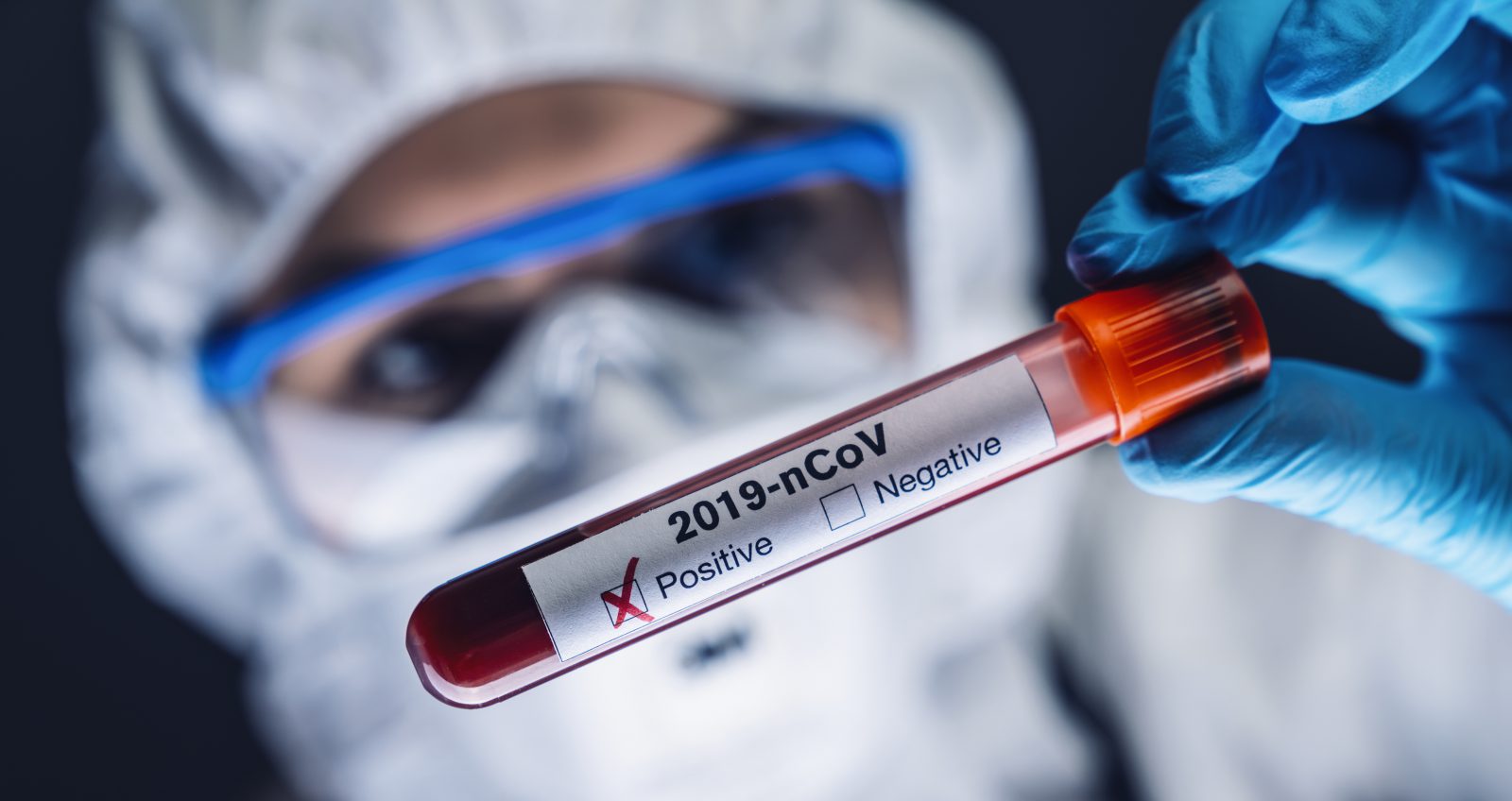
Project Size
$105K
Duration
3 Weeks
Project Team
2 Project Managers / 6 Design Engineers
Industry
Automation Machine
“
The Machine Design Solution

Sterling Engineering’s team included 2 Project Managers who liaised between the client’s lead engineer and SEI design engineers. Project managers coordinated the design and detailing effort between 2 shifts that worked around the clock to compress the delivery schedule.

The system was designed with Solidworks 3D-CAD assembly models and detailed part drawings. These tools allowed Sterling Engineering to verify station operation and fitment into the overall system resulting in a safe and efficient process layout.

At the kick-off meeting, Sterling Engineering worked with the client to analyze the source data of similar stations and apply the knowledge to design the new stations for this particular application.

Because of the size of the design team required, Sterling Engineering’s team focused on producing the individual stations and locating them in the main machine layout, full assembly drawings, bill of materials, and detailed part drawings for release to manufacturing.