Project Snapshot
Our Client, the Director of Engineering for a global logistics company, had new technology that could be a game changer for some of their locations. As corporate in-house engineering was already over capacity on existing projects, Sterling Engineering was engaged to support remote Feasibility Studies. Sterling was able to optimize the engineer’s time and knowledge efficiently in weekly online/remote design reviews.
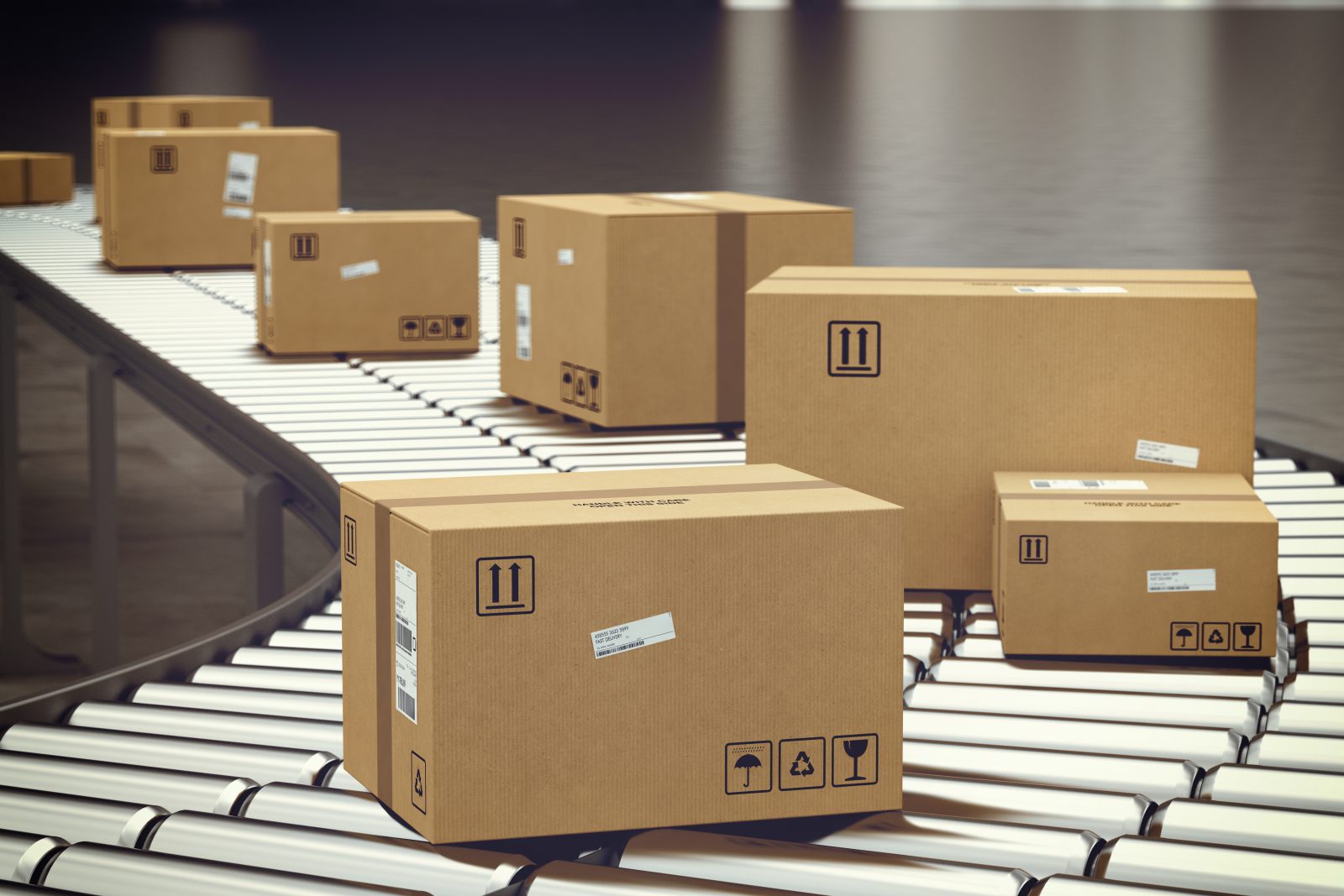
Project Challenges
- The client operates one of the world’s largest ground package distribution facilities for a mail /parcel logistics company. The facility is over 1.5 million square feet and has a perimeter of 3.1 miles, with over 65 miles of belts and conveyors used to automate the sorting of packages.
- Packages are only handled during loading and unloading. All sorting takes place through a system of conveyor belts and push paddles, utilizing high-speed cameras to read the destination from a smart label to sort a package to its route.
- The facility sorts approximately 1.6 million packages per day. During the months of November and December, volume can exceed 3 million packages per day.
- Our scope was to provide automation design options for modernization and max capacity for 4 key areas within the facility: Primary, Outbounds, Small Sorts, and Irregular.
- For each designated area, Sterling’s scope of work included recommendations for changes to existing layout, replacements of legacy equipment, upgrades of existing equipment, ROM cost estimates for all options, and validation of maximum capacities.
Sterling's Solution

We have the advantage of “boots on the ground” to support field surveys, plant audits, and site drawing verification. Our team was on site within two weeks of the PO. We met the site specialist and collaborated to determine best locations for this new technology, the integration locations for feeds and returns, and any obstructions.


